End-of-Line Test Bench 32 DCVs: Highest quality assurance for our customer.
Task: | Realisation of an automated EoL test bench for 3/2 Directional control valves of cooling circuits for cars | |
Department: | Assembling | Smart Production | |
Business: | Automotive |
For a developer and producer of high-quality mechatronic components for the automotive industry, our experts at VESCON Systemtechnik developed an automated test bench for their production.
Here, the test items are carried to the individual test stations by robots, OK tested components are provided with a DMC code and placed directly into customer containers. The company's own tracebility and PDA software SO3 Hiberion is used to control as well as store all measured values for complete traceability.
Due to the successful and satisfying handling and functionality VESCON has already been assigned with a new project for our customer - further orders in the field of valve assembly can be expected.
Services provided by VESCON:
- Software engineering PLC
- Construction & Assembly
- Production data acquisition
- Commissioning
- Service & Training
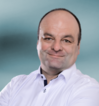
See further with VESCON: Headlight assembly line for the new "eyes" of the BMW 7 model.
Task: | headlight assembly line | |
Department: | Special machinery engineering | Automation | |
Business: | automobile industry |
Drivers and owners of the new BMW 7 model enjoy state-of-the art light technology, not least owing to the assembly lines designed by VESCON. ZIZALA Lighting systems has developed a LED headlight and a unique "searchlight" for BMW which is produced in Austria. Thanks to our long-term experience in the field of light technology VESCON has been able to contribute to the successful production and high quality of the new "eyes".
As in the automotive industry the headlights have become a major design feature and are increasingly based on LED technology, the assembly processes are getting more and more complex and demanding. The result is that ever higher demands are placed on the plant constructors not only regarding control technology and ESD protection, but also with respect to the use of material having direct contact with the product during the assembly process and the total logistics operations around the plant. This implies the necessity for tracing batches and individual parts during the assembly process.
With more than 100 different components, such as boards, heat sinks, light bars, reflectors, and design trims, being involved and the assembly processes becoming increasingly complex due to this large number of parts, the headlight assembly line constructed by VESCON is the largest one ever used at ZIZALA.
The headlights are assembled and checked in line passing 15 partly or fully automated stations. The respective assembly processes like screwing, pressing or lasering run automatically. At the end of the assembly line the headlight is adjusted and the light pattern is tested automatically. After that the headlight is conveyed to the fully automated robot station where the adhesive bed is activated and the sealing and adhesive substance is applied by the robot. Then the pane is inserted and the completely assembled headlight is subject to a leak test. At the end, only 100 % tested headlights will leave the plant.
The newly developed "searchlights" that can be supplied on demand are also produced on a plant designed by VESCON. Thanks to an intelligent software and the on-board electronic system these headlights can identify obstacles at the roadside and illuminate them if they represent a potential source of danger. This assembly line as well has been produced at VESCON as a turnkey solution and then put into operation on the customer's premises.
Services provided by VESCON:
- concept development
- development and construction of a turnkey plant
- training courses
- production support
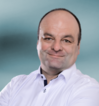
More power with VESCON: Turbo assembly line at BoschMahle Turbosystems.
Task: | turbo assembly line | |
Department: | special machinery engineering | Automation | |
Business: | automotive industry |
For economic reasons the downsizing of motors has become a decisive issue in the design of new automobiles and engines. As a consequence, the development focuses on the charging of ever smaller engines assigning a significant role to the use of turbo chargers.
For the Austrian production plant of BoschMahle Turbo-systems VESCON has designed and realized several plant concepts. This project included among other things the development and construction of an automatic picking machine which pre-assembles the small and delicate components supposed to be installed in a high-speed turbo charger in an assembly tray. These trays are then used in the fully automated assembly line. The individual components are stored in specifically designed revolving magazines and separated. This allows an uninterrupted production, as the individual cartridges can be reloaded from outside. The separated parts are placed in the tray via several axis systems. In addition, the data of all individual parts are read in via data matrix codes during the assembling process which guarantees the consistent tracing of the components.
In another plant developed by VESCON, where the pre-assembled trays are also employed, special chargers and turbo chargers for utility vehicles are produced in small quantities. As also for these chargers the same standards concerning quality and data tracking are demanded, we had to focus intensely on the measurement system capability and the process safety considering at the same time a higher degree of manual operations. In some sections manual operations alternate with fully automated processes. This coupling could be realized in a concept which had already been implemented several times before. Here, as well, all pressing, screwing and testing operations are recorded and the individual parts are conveyed to the plant while being batchwise monitored. The entire data are transferred to the internal PDA system and filed.
Thanks to easily replaceable and coded installation kits a rapid change to other types is possible which makes this concept highly flexible.
Services provided by VESCON:
- concept development
- development and construction of several turnkey plants
- training courses
- production support
- maintenance and servicing

VESCON provides motion: Assembly line with EOL test bench for VW rear axles of the VW Caddy 4motion.
Task: | assembly line with EOL test bench | |
Department: | special machinery engineering | automation | |
Business: | automobile industry |
Within a period of 27 weeks - from order to delivery - VESCON has developed a turnkey assembly line for rear axles for the VW or MAGNA engineering centre in St. Valentin. The challenge was to guarantee a high flexibility allowing the personnel to take strong influence on the process when handling different production quantities on the one hand, and to ensure the same process safety and measuring system capability as with fully automated lines on the other hand.
The plant has been designed in such a way that a worker can either "walk along with" the axle through the production process, or - in case of a higher production volume - pass the workpiece carrier on to the next worker. Depending on the customers' call-offs one up to 6 workers can operate the plant.
This required the development of a PLC higher-level production data acquisition solution (PDA) including an interface to the internal SAP system. In the PDA system all process parameters, results and personnel data are recorded.
In the first plant section the raw, painted rear axle as well as bevel gears and crown wheel are measured via an integrated Zeiss measuring machine. Then follow the assembly of the gearbox and the backlash and friction measurements as well as the assembly of the half-axles and the wheel hubs with brake discs. After this the Haldex clutch is fitted. Of course, torques and rotation angles in the screwing processes and pressing forces and ways in the pressing processes are recorded and controlled as well. The quality-relevant processes like measuring, pressing and screwing as well as the test run take place in a fully automated way. By indication via the PLC unit the worker is guided through the workflow and has to confirm the completion of the individual worksteps.
The finished rear axle is filled with two different oils on the EOL test bench before it has to undergo the test run (Haldex, gearbox, ABS sensor system).
During an iO run the axle is finally embossed and the corresponding assembly and test records are created. By this procedure it is guaranteed that the driven rear axles in the VW Caddy 4motion run smoothly and to the customer's satisfaction.
Services provided by VESCON:
- concept development
- development and construction of a turnkey plant
- process data acquisition (PDA) with SAP interfaces
- training courses

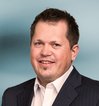
Division Head Software Development
Phone +43 3112 36006-400
martin.feichtgraber@vescon.com
In the service of health: A new assembly line for Roche Diagnostics Graz GmbH.
Task: | planning and construction of an assembly line for the production of a novel blood analyser | |
Department: | special machinery engineering | automation | |
Business: | medical technology |
After years of development activities and the respective number of test runs Roche Diagnostics Graz GmbH was finally in a position to release the company's newly designed blood analyser onto the market. The „Fluidpack“ is used primarily in intensive care units for determining the patients' blood values before adjusting them correspondingly. Thanks to its novel and compact structure the Fluidpack can be replaced by the intensive care nurses independently and without the help of the service technicians when the analysis liquid has been used up. This is not only a significant improvement with respect to convenience and user-friendliness, but also a major factor in saving costs.
Of course, these highly sensitive measuring devices called for a corresponding assembly and test plant. VESCON scored with a concept meeting the specific demands in terms of mechanical design and software equipment and finally received the order for the planning and implementation of the assembly plant with a higher-level PMS system communicating with the customer's quality database.
During the construction of the plant major importance was assigned to the selection of the materials and the compatibility of a partly automated plant allowing operator influence with the highest possible protection of the sub-processes. This could be ensured by a corresponding personnel management via PLC on the one hand and the tracking of component and process data on the other hand. Thus the uninterrupted recording and allocation of the production data via the serial number is guaranteed.
The plant combines automated production and assembly technologies as well as high-precision measuring processes with several operator stations. In the meantime the plant has been duplicated and is used at another location of the Roche Diagnostics International AG.
Services provided by VESCON:
- concept creation
- development and construction of a turnkey plant
- development of a tailor-made PMS system
- training
- production support
- continuous plant maintenance and servicing
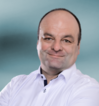